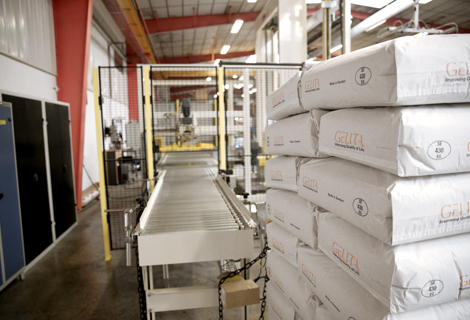
Two robots remove heavy lifting and increase production
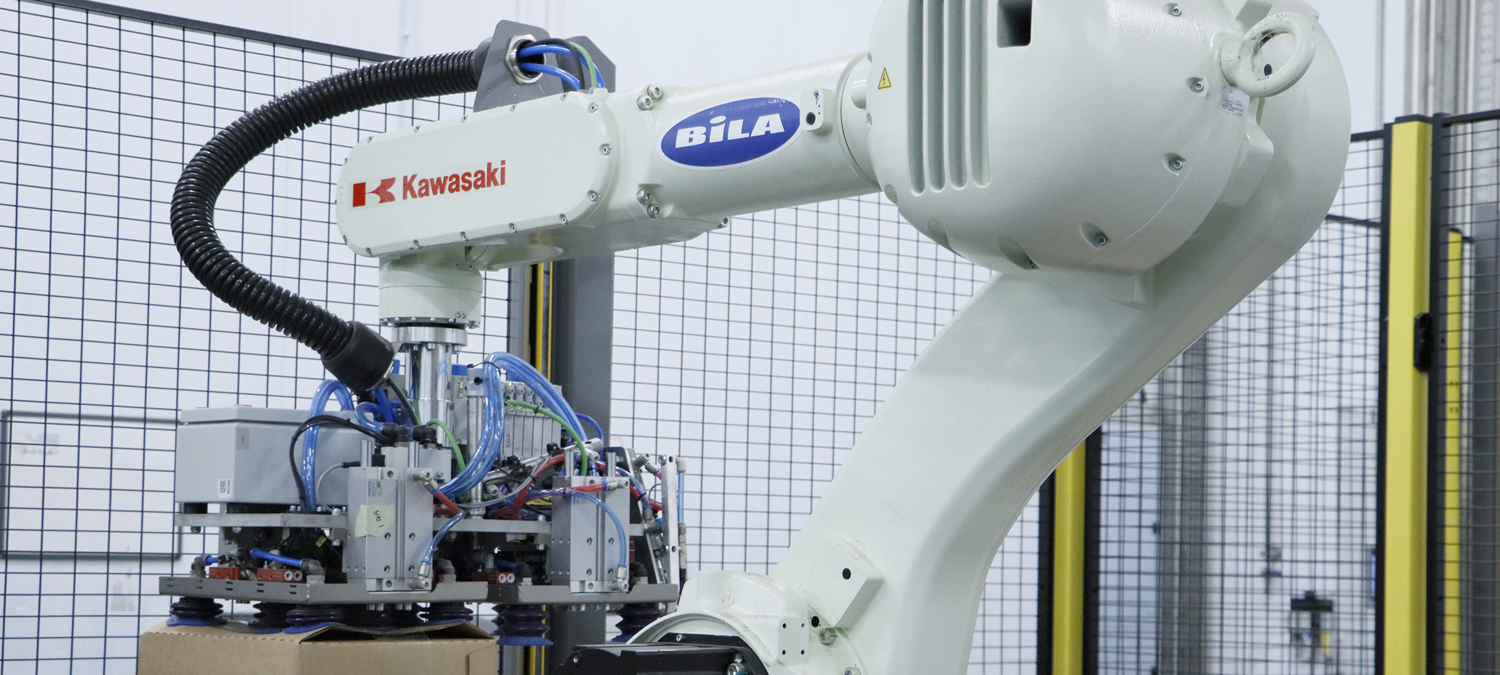
Palletising solution improves conditions
Lakeland Dairies in Northern Ireland has installed two robots from DAN Palletiser to assist in their end-of-line production of butter blocks. The robots are designed to ensure efficient and precise palletizing of numerous butter blocks annually, varying in sizes and packaging. Although the implementation took some time, the robots have been running seamlessly since then, leading to the development of new automation solutions from DAN Palletiser.
Improved physical work environment
New production opportunities
Close cooperation
Increased production capacity
Challenge
Manual system that was very labour-intensive and required a lot of heavy lifting from employees.
Solution
Two robots intended to ensure efficient and precise palletising of butter in blocks in various sizes.
Benefits
Increased production capacity and improved working environment.
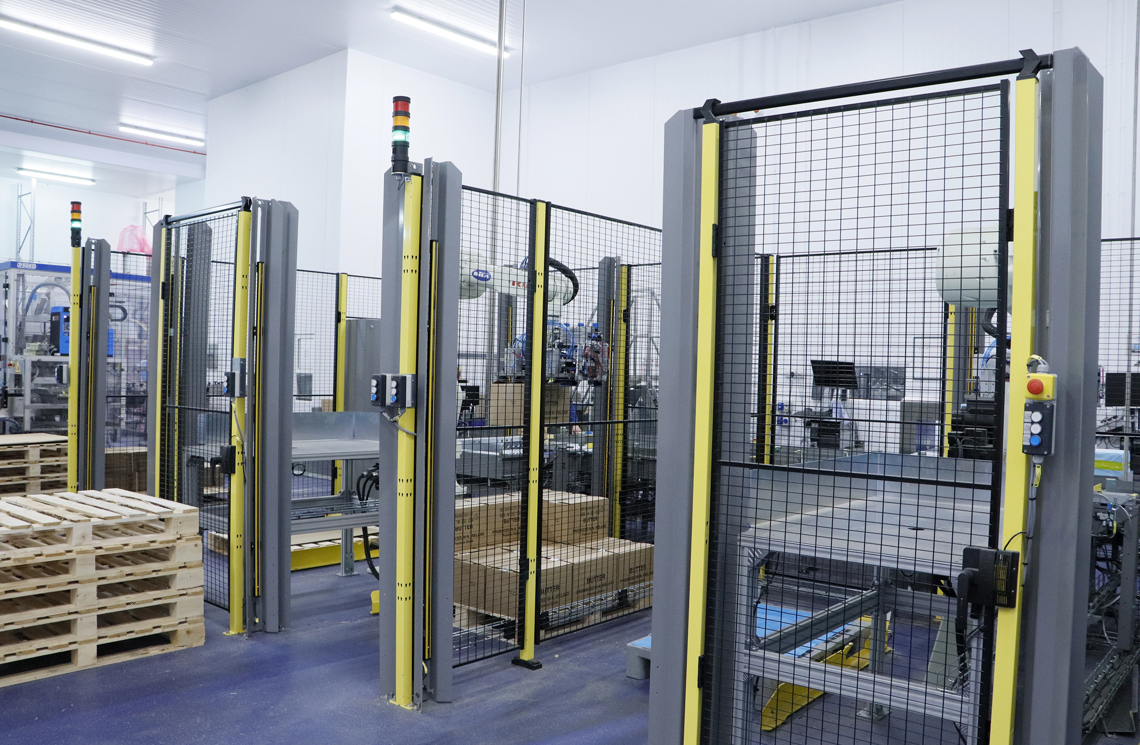
Lakeland Dairies and DAN Palletiser have had a longstanding collaboration that began in the 90s at a factory in Newtownards with a pallet loader. Since then, the partnership has only grown stronger. Lakeland also utilizes some of DAN Palletiser's products at one of their facilities in County Londonderry, and here in Ballyrashane, they have a brand-new robot system installed.
The robot system handles the palletising for their new butter production line. The collaboration for this new line began about a year and a half ago. Last summer, the final details were ironed out, and the robots have now been installed and operational for approximately four months in conjunction with the new butter line.
”The robots run flawlessly and have elevated our production,”
David Smyth, Engineering Project Manager at Lakeland Dairies
Two robots have been installed to support the two end-of-line production lines with butter from the production. The butter is conveyed on rollers and is then picked up by the robots using a suction cup head and placed on pallets. The robots can handle various types of butter blocks, but usually, it's 25 kg butter blocks that need to be palletised. The two robots palletise approximately 720 butter blocks per hour. When a pallet is full, an employee, using a pallet lifter, moves the completed pallet and replaces it with a new empty pallet. The employee then transports the pallet to a pallet wrapper, where it is prepared for shipment.
This process also holds a future for DAN Palletiser and Lakeland Dairies, as both Simon (COO at DAN Palletiser) and David agree. The two new robots have assisted in production by replacing much manual work. Previously, everything was done manually, and employees had to manually lift the large 25 kg butter blocks onto a pallet. "It can involve many heavy lifts 24 hours a day, seven days a week," says David.
Therefore, DAN Palletiser and Lakeland are already in the process of expanding their collaboration. Lakeland aims to become even more adept at automation to further enhance their production levels and simultaneously eliminate more manual handling. This approach not only improves their working environment but also reduces strain on their employees.
”Working with DAN Palletiser has been very productive so far, and we have a good partnership. We foresee a future collaboration on more of their products in our production,”
David Smyth, Engineering Project Manager
Therefore, in the pipeline, there is a new robot, a fully automated stretch wrapping system, and a Global AGV truck. This setup will support the two existing robots. With an additional robot, production can be further enhanced. A self-driving AGV forklift will be available for the three end-of-line robots, allowing them to bring in new empty pallets and transport the finished pallets to an automatic stretch wrapping system, preparing them for shipment.
"It has been a longstanding collaboration with Lakeland, and we have been very pleased with the partnership and the support and trust that have been present throughout from Lakeland," tells Simon Rune Sørensen, COO at DAN Palletiser.
The significance of this collaboration for both parties has been to explore possibilities—specifically, the potential to automate a manual system. The previous manual system was labor-intensive, requiring substantial heavy lifting from employees.
Cases for inspiration
With dedicated employees, we ensure efficient service at the highest level, regardless of where you are in the world.
Call us at +45 58 38 21 93
Contact us
We are ready to answer your questions
as well as take a non-binding talk about
the possibilities for automatic
palletising in your company.